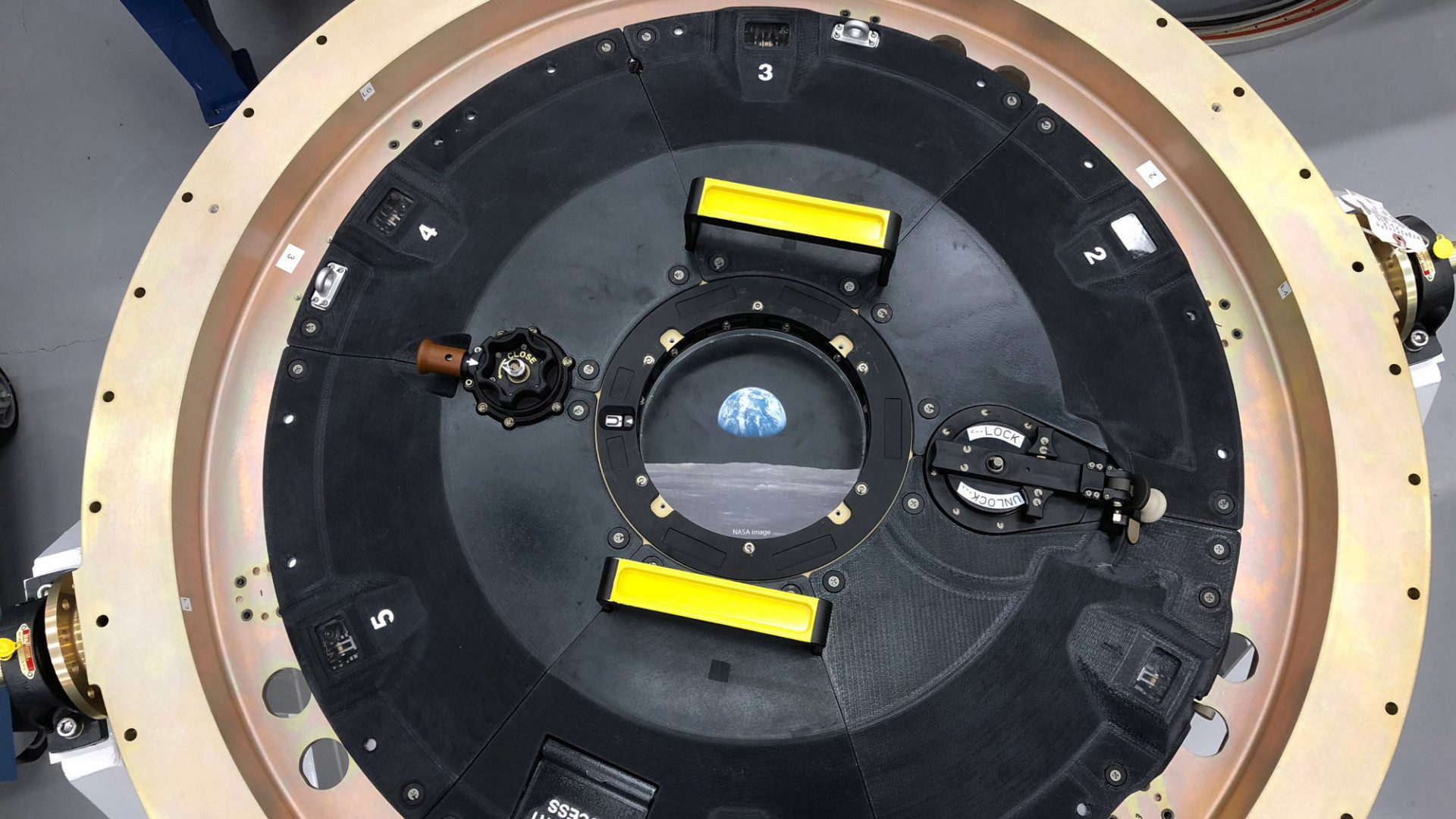
NASA’s next venture into deep-space capsule will feature additive manufacturing in a big way. The agency’s new Orion capsule will incorporate more than 100 3D printed parts, which will be produced by Stratasys in collaboration with Lockheed Martin and PADT.
Exploration Mission-1 (EM-1) is Orion’s — NASA’s new deep-space capsule — next test flight, launching in 2019. The spacecraft will fly to the Moon (not quite infinity) and beyond. EM-1 will be the capsule’s first text launching atop the Space Launch System — thought to be the world’s most powerful rocket. This flight will be un-crewed.
If this flight goes to plan, then EM-2 will follow, this time with astronauts on board. It will be the first manned flight near the Moon since 1972, and serves as a preparation for more complex missions in deep space.
A key component in the construction of Orion is more than 100 3D printed parts, including critical components that sit outside the capsule’s docking hatch. These elements, referred to as “next-generation 3D printed parts” in a release, could mark a step change in additive manufacturing for aerospace.
The joint effort by 3D printing specialist Stratasys, defense contractor Lockheed Martin and engineering firm PADT demonstrates a crucial factor in spaceflight engineering — repeatability. This is achieved for the Orion capsule with Stratasys’ Antero and ULTEM 9085™ materials.
“Working with PADT, Stratasys, and NASA has enabled us to achieve highly consistent builds that move beyond the realm of prototyping and into production… We’re not just creating parts, we’re reshaping our production strategy to make spacecraft more affordable and faster to produce,” said Brian Kaplun, Manager of Additive Manufacturing at Lockheed Martin Space.
Not Just a Prototype
Instead of simply using the technology for prototyping, the three companies are using the machines to create scale production parts. The technology’s benefits are that it can produce high-performance lightweight prints both quickly and cheaply.
With Stratasys 3D printers and materials producing the parts at Lockheed Martin’s Additive Manufacturing Lab, the result is precision parts with high performance mechanical, chemical, and thermal properties.
“The demands of space travel require extremely high performance materials and the most rigorous manufacturing processes in the industry. Part integrity and repeatability are essential and must pass NASA’s demanding testing and validation process. Based on decades of experience delivering strong and lightweight additive manufacturing solutions for leaders across the aerospace industry, Stratasys technology is ideally suited to match the high-reliability manufacturing processes required for production parts in space exploration,” said Scott Sevcik, Vice President of Manufacturing at Stratasys.
Find about more about the NASA’s deep space exploration systems on its website.
Source: Stratasys
(Top image: Business Wire)
Website: LINK
Schreibe einen Kommentar
Du musst angemeldet sein, um einen Kommentar abzugeben.