BMW and MIT’s Self-Assembly Lab have collaborated to develop “liquid printed pneumatics”, the first reported 3D printed inflatable material that can morph from one state to another and expand into any shape or function.
Just around two years ago, the BMW Design Department and MIT’s Self-Assembly Laboratory began a cross-disciplinary study with the mutual goal to push the boundaries of material technologies.
In the midst of this collaboration, the automotive pioneer and prestigious university lab have successfully developed “liquid printed pneumatics”, which are 3D printed inflatables that can morph into nearly any shape or function.
Inflatables are extremely useful for a number of applications, from packaging to the interior of vehicles. Unsurprisingly, BMW is focusing on the latter, while MIT is taking a more universal look at adaptive interiors. Both are also aiming to revolutionize the future of comfort inside of autonomous vehicles.
Their resulting work will be on display at an exhibition called The Future Starts Here at the V&A Museum in London. The showcase is all about exploring the power of design in shaping the world of tomorrow, a theme that MIT and BMW have accumulated a lot of knowledge on through the collaboration.
BMW’s head of brand vision and brand design, Martina Starke, said: “We are proud to be one of the contributors to show our achievements. The ’Liquid Printed Pneumatics’ project is a perfect example for a fruitful cross-disciplinary collaboration we’ll see more and more over the coming years, especially at BMW.”
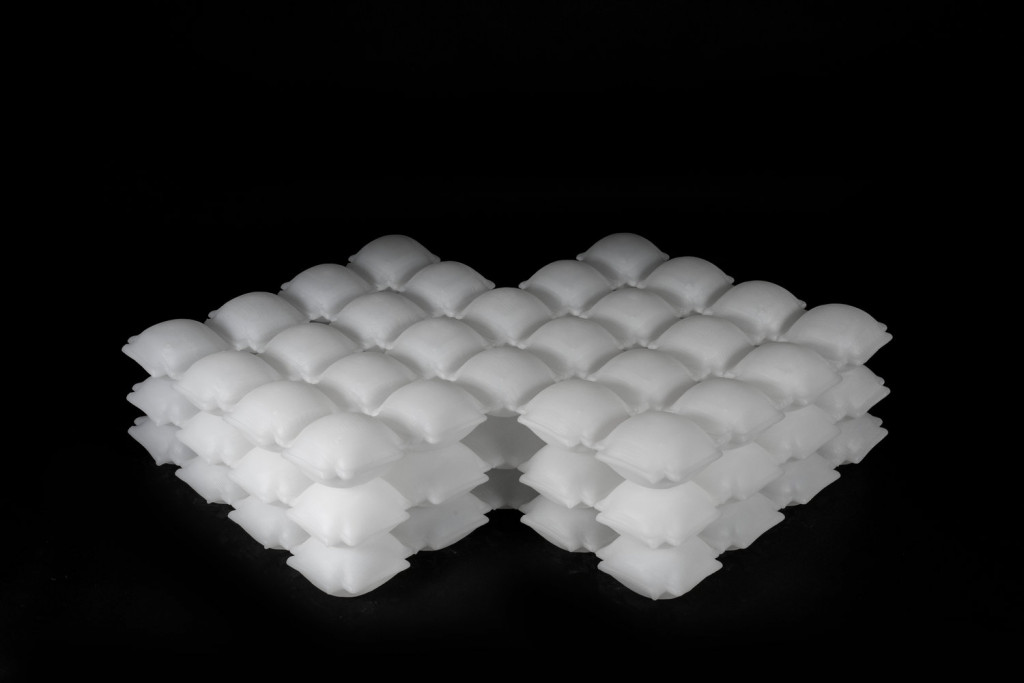
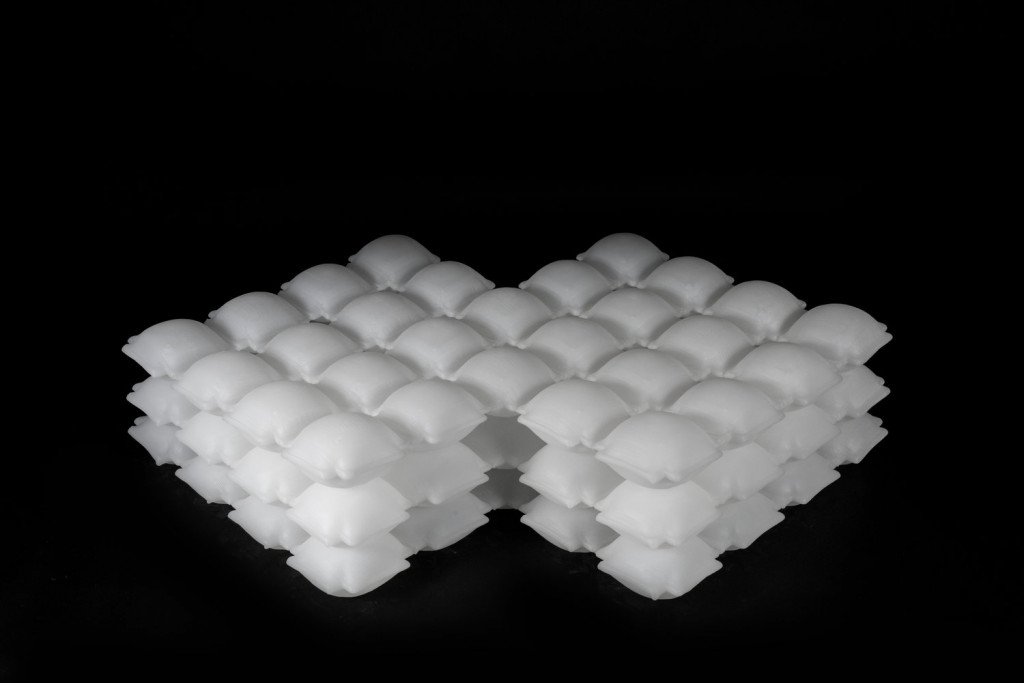
Liquid Printed Pneumatics to Make Car Rides Comfier
These advanced liquid printed pneumatics were developed by depositing liquified materials such as rubber, foam, or plastic into a vat of gel. The 3D printed shape remains in place until it hardens. The gel keeps the liquid in place, making it possible to create larger or more complex objects than your average 3D printer is capable of.
To create these liquid printed pneumatics, the researchers used 100 percent silicone rubber and 3D printed complex, inflatable designs that are equipped with air chambers. These chambers enable different areas of the print to inflate and move at different times, where the inflation takes place is fully dependent on the amount of air pressure within the system.
Skylar Tibbits, co-director and founder of the Self-Assembly Lab, explains the process in slightly more computational terms: “It’s programming it with air. Instead of zeros and ones, you’re sending different pulses of air.”
The resulting characteristics of these silicone-based objects appear ethereal and relaxing, certainly not qualities which are usually associated with current automotive design. But when it comes to innovation, both BMW and the MIT Self-Assembly Lab are consistently ahead of the pack, and together they’re planning to integrate these groundbreaking materials into an autonomous vehicle near you.
If you’re in London between now and November 4th, 2018, be sure to pay a visit to the Sainsbury Gallery at the V&A Museum to see the Future Starts Here exhibition and inflate your curiosity.

Source:MIT Self-Assembly Lab/Fast Co.Design
Website: LINK
Schreibe einen Kommentar
Du musst angemeldet sein, um einen Kommentar abzugeben.