All3DP travelled to Hannover Messe 2018 to witness the unveiling of the new Ultimaker S5 3D printer. To learn more about this professional-grade 3D printer and the company’s refined focus, we sat down with to Siert Wijnia, the co-founder of Ultimaker; and Paul Heiden, Senior VP of Product Management.
Back in 2011, a Dutch 3D printing company called Ultimaker was born out of frustration over the inability to get a RepRap Darwin 3D printer up and running. That year, the Ultimaker Original was released to the world. As one of the first-ever desktop 3D printers to hit the market, this small, wooden framed 3D printer was only capable of printing at 20 micron resolution on a 21 x 21 x 20.5 cm build volume.
Nonetheless, it’s mere existence helped jumpstart the desktop 3D printing revolution that we currently see today.
Although much has changed over the last seven years, Ultimaker continues to lead the industry with its open-source 3D printing ecosystem. Long gone are the days of 3D printers with rinky-dink wooden frames. Instead, Ultimaker is now focused on manufacturing 3D printers that are accessible, reliable, and designed for the professional environment.
Released in 2016, the Ultimaker 3 quickly became one of the most coveted professional-grade desktop 3D printers on the market. This groundbreaking machine offered dual-extrusion capabilities, swappable print cores, and an all-around intuitiveness that were unprecedented at the time.
The open source 3D printing pioneers are now back it again, recently releasing the bigger and better Ultimaker S5 3D printer. It has a generous build volume of 330 x 240 x 300 mm, dual extrusion capabilities, as well as an improved feeder system with a filament flow sensor that automatically pauses prints when filament runs out. Priced at just under $6000, Ultimaker is clearly targeting its new 3D printer at the professional market, hoping to capture the attention of designers, engineers, and businesses both big and small.
Read more: Ultimaker S5 3D Printer: Review the Facts
All3DP was in attendance at the industrial manufacturing trade show Hannover Messe 2018, which is the setting that Ultimaker chose to unveil the sleek Ultimaker S5 3D printer.
Although the gathering was centered around the Ultimaker S5, the company had a laundry list of other product releases and collaborations. The Ultimaker team also announced Ultimaker Tough PLA, a material that strives to replicate the mechanical properties of ABS, without the toxic fumes. There’s also the new Ultimaker App, a mobile app that allows users to remotely monitor and stay update on their printing progress. Additionally, Ultimaker also revealed a massive collaboration with some of the top chemical producers in the world, which will lead to the development of print profiles for the Cura slicer.

After a brief press conference filled with excitement, we had the pleasure of sitting down with Siert Wijnia, the co-founder of Ultimaker; and Paul Heiden, Senior VP of Product Management; to talk more about Ultimaker S5, the company’s narrowing focus on the professional market, and how the 3D printing industry is changing before our very eyes.
How did the transition from the Ultimaker 3 to the Ultimaker S5 take place?
Paul Heiden: In 2016, we introduced the Ultimaker 3. And it sort of surprised us. In the beginning, we didn’t really see how fast it was being adopted in the professional market. So, once we got that, in several months, our distributors were saying there is something going on. We started to do market research. And, as part of the market research, we found, in early 2017, several annoyances, really irritating things. Things that have to do with material handling. It has to do with better adhesion, and several of these things. Now, we can’t solve everything at once, but we were planning to have a bigger machine anyway.
We wanted to ensure that all of the elements that would contribute to the liability, to zero hassle, could actually be adopted. One of the biggest issues was implementing a touch screen, instead of the wheel. It’s just faster. We also invested quite a lot in better adhesion. You can’t really see it, but the whole bed leveling system has been vigorously improved. We also decided to add, somewhat later in the market, an aluminum build plate for better adhesion with engineering materials. So, step by step, we tried to improve many aspects. And we felt this is the point where we have a machine that’s fundamentally better.
Does the Ultimaker S5 symbolize a larger focus on the professional market?
Heiden: This printer is built for the current professional user, which are predominantly found in small and medium enterprises. But it’s also meant for the larger devices. And what we did, over the last year, we organized the Business Development Department, and we simply sat down with these larger companies. We quickly found out that they like to standardize on one 3D printer, being ours. They like to have at least some services around it like, at least for some continuity, warranty that things are already apparent. And I think the wonderful thing is that we think we’re the only one with a complete ecosystem, and we’re the worldwide with an operating set of distributors, we’re able to deliver anywhere.
One of the things we’ve heard from one of the customers running a Design Department was, “look, I’m not paying my people to tweak. I’m not paying my people to have fill printers. I just want to get this done.” Printing, in itself, is not important. The object is important. And that really made us speed up everything around zero hassle. So, the more professional the user, the less willingness they have to accept additional handling errors and so on. It’s not allowed.
Why did you decide to expand the build volume of the X-axis instead of the Z-axis?
Heiden: That is easy. Everybody can put plastic on top of plastic. We started this in 2016 and we said everybody can go up, so we need to go like this. We need to go into the X axis width and start to improve that. And it took an awful lot of time and understanding of technology, even to go the 33 centimeters that we’re currently dealing with.
Is the Ultimaker S5 the first of a new 3D printer product range?
Heiden: Yeah. I think it’s fair to say that we’re number one when it comes to the office environment. And what we’re trying to do with the S, which stands for Studio, is completely focus on that environment. So, what people are asking for is clean hands, zero failure, the ability work from your desk. Things like Cura Connect allow you to just push print jobs into a cue. So, that’s the sort of thing we’re aiming for. At the same time, we’re looking into environments that are far rougher. We like to talk about the concrete floor where you have machines that should be able to perform in a workshop and next to CNC and so on.
And that’s the other environment. We’re not there yet, but that’s the other environment we’d like to go to. But this is a focus on zero hassle, full deniability, clean hands, no poisonous stuff like what SLA or SLS will bring you. We’re pretty sure that this is the right guidance.
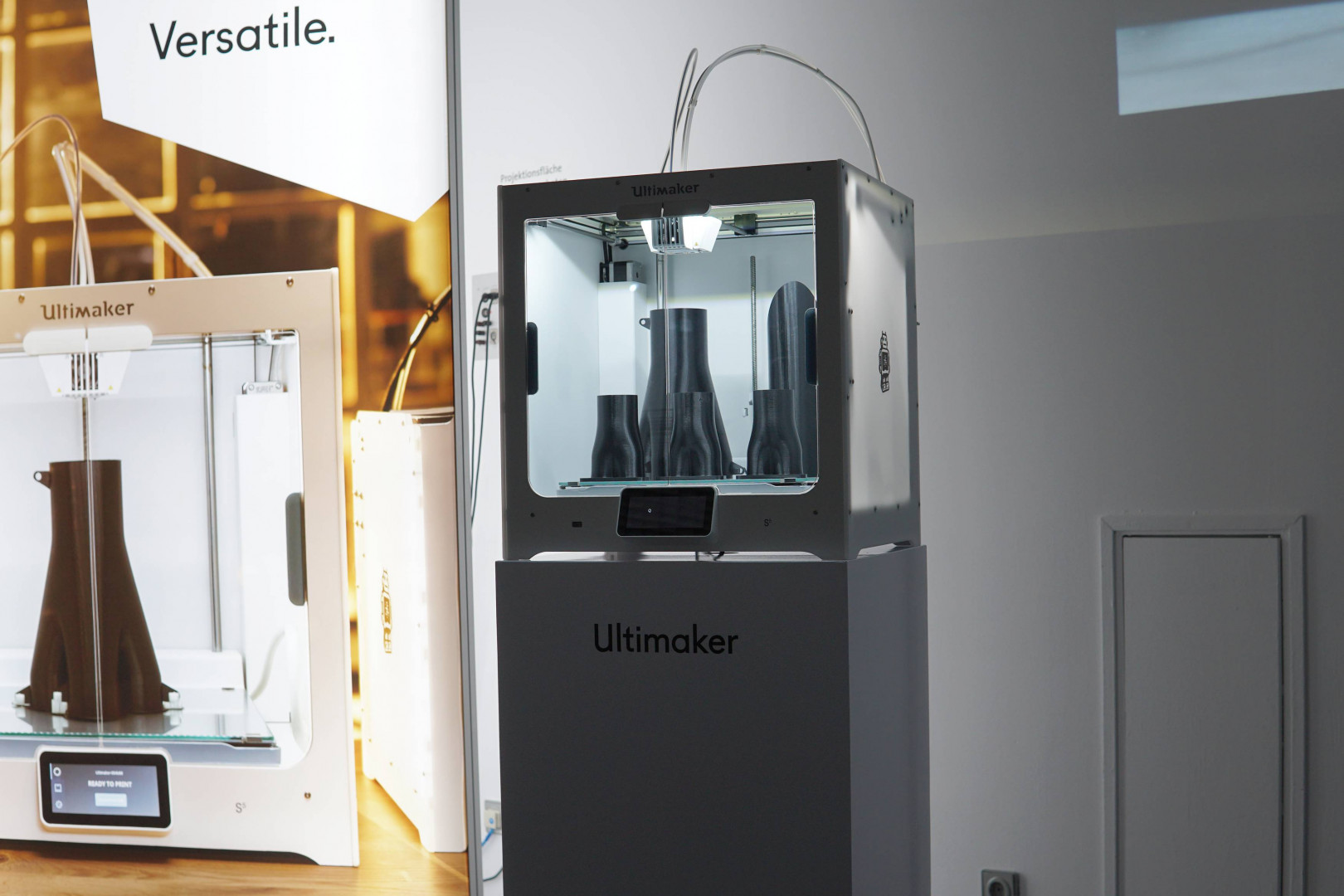
What do you mean when you talk about Ultimaker being a future-ready ecosystem?
Heiden: I’d like to focus probably on two things – no, three. One, you will see print force that support other materials. But with the collaboration with chemical companies results in different materials that we need to adopt, I’ll tell a little bit more about that later. But we will see new in force. That was the whole point of having the print core for specific purposes, specific prints. The second is that we will soon come up with drastic improvements in material handling. I wish I could say a little bit more, but I find it a fascinating idea, and we’re working on it to get it released soon.
And thirdly, from the end of 2016, once we understood what was going on with our machine, we started to invest in other products. So, we introduced SDK, software development kits, to simplify the creation of software between Cura and 3D software like CAT or CT scan or that sort of software. And another one, which I like to call the material development kit, is a piece of software that helps these chemical companies to create printing profiles for their materials.
And I was discussing it, once we understood that there are about 70,000 different plastics in the world, A) a clogged material system doesn’t work, and B) somehow, we cannot make all of these print profiles. So, the whole idea of creating software that will actually help material suppliers create printing profiles has really been a breakthrough. And it’s an elephant. We’re talking about a difference between six months of print profile creation versus one or two weeks. So, that really matters.
How did the recently announced collaboration with large chemical companies come about?
Heiden: I’ll tell you a little story. When I started at Ultimaker, we had about 80 people, and we were building a nice machine. That was it. Somewhere, in the end of 2016, suddenly, chemical companies came knocking on our door. At the beginning, I was honored that these people would come to us from the large companies. And then, at a moment in time, I thought this is not normal. What’s going on?
And then, it appeared that all of these companies have basically been forced by their customers to bring filament to the market made from the same material that they would use in pellet form for mass production. So, what these companies are saying is that you can only deliver for mass production, your materials for mass production, if you ensure that it’s also available for our development tooling being 3D printers. And that’s how it all started. To be honest, these chemical companies weren’t happy, but making filament is something they need to do now.
They need to do that in order to ensure their involvement in the complete development towards mass production. That’s why they want to. And then, we came up, and that was coincidental. We were already thinking about this material development kit. And, suddenly, it changes for them. Suddenly they thought ‘so, if we make filament, we create our own printing profile, and it takes us a few weeks instead of a month.’ Now, it becomes viable. And that’s how everything starts. Since 2017, we’ve worked very hard to get everything done well.
And you probably could see the relief in my face that it is now done. Of course, new material suppliers will continue to access this ecosystem. But this is where we want to start.
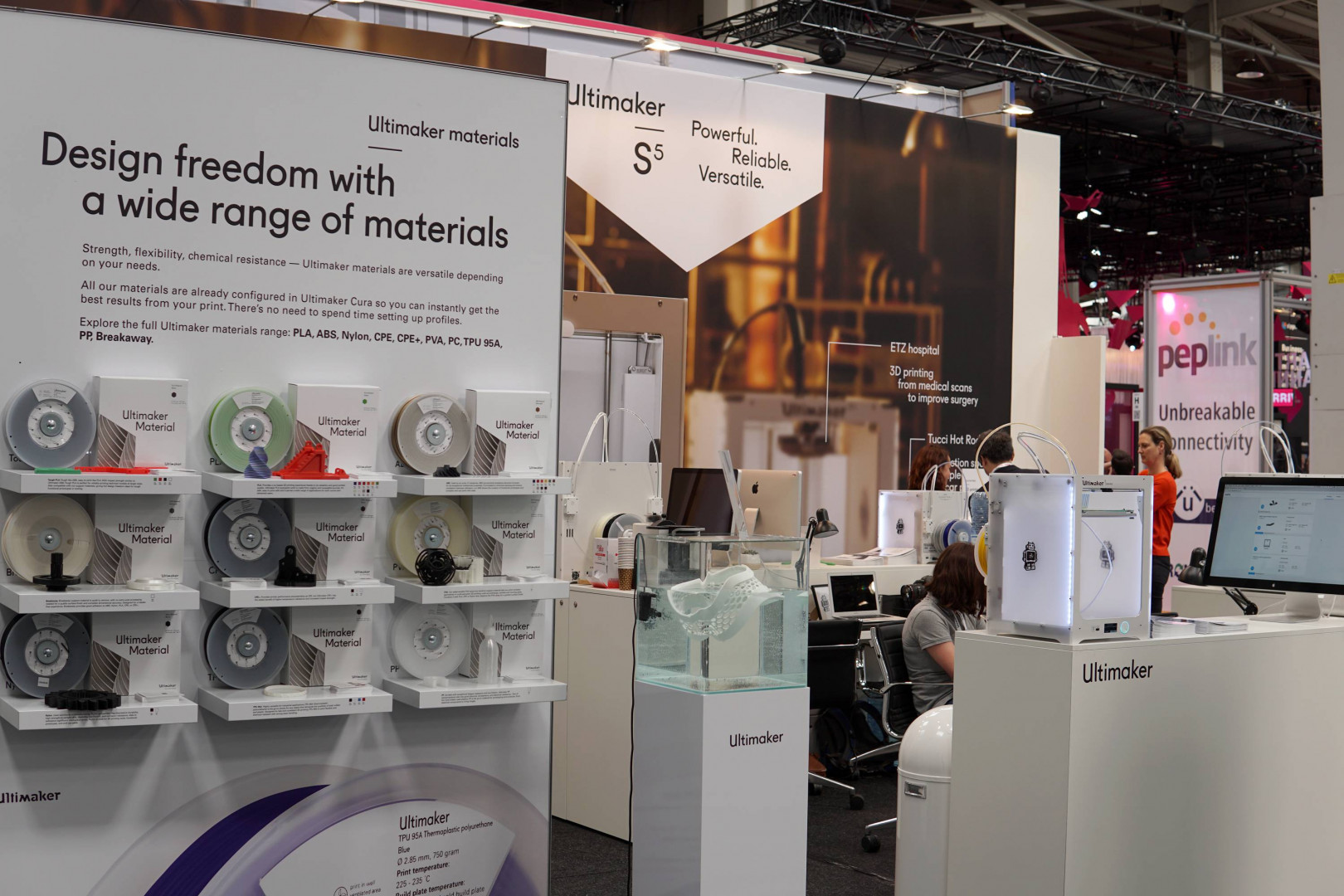
How will the new Ultimaker App enhance the company’s 3D printing ecosystem?
Heiden: When we introduced Cura Connect, that was the first step for us in machine management. So, it would automatically create a network and allow you to start the cue. The cue is marked meaning that the print job determines what printer needs to go with the right print core and the right materials and so on. And then, what we realized that we essentially had a mobile website as an app. So we decided no, that’s not what we’re going to do. The new app must completely support Cura Connect. That way, you can see in the cue what’s going on from anywhere.
And, finally, we’re now able – we’re always working in a high security environment. BMW does not allow you to do all sorts of things on the web. So, what we’re trying to do is add some value that will not destroy security. And so, one of the things that we added in the app is notifications. So, when you’re in the training, and the filament flow decides to stop, you will know right away. It’s not nice that you get it, but at least you know. You know that you need to go back in order to have your object ready by the next morning.
What is the current mission of Ultimaker?
Siert Wijnia: Our goal is really to make it look simple because that makes it for people not to be scared to use it. So, if you had to program your phone before you could actually start it up, if you were running that phone as a system as it is without the official interface, you would be scared of the phone and not use it. The happy few that were not scared would probably like it that way, but it’s not me. So, take away that level of making it accessible. It sounds very simple but making it as easy as possible is what makes it a success or not.

Have you enhanced the dual-extrusion process from the Ultimaker 3 for the S5?
Wijnia: That was implemented directly, but it’s a continuous effort for all of the printers to make them even more reliable. So, there is a continuous effort on the algorithms that are in the slicing software that make it a better result, that make it more reliable. And, on the outside, maybe you don’t see it. But it could influence the layer quality or adhesion, or tons of other things. But the dual extrusion runs on the same hardware, the same technology. So, any improvement that we make for Ultimaker 3 is also implemented for the S5.
I will tell you the biggest one, and it’s not the machine itself, but how we handle that as an organization. We know what we do, and we know how we can do it, and know how to get there. And that is, if you compare that to seven years ago when we just opened the box again because someone said this part is no good, that is different. That is something I can tell from the last seven years, huge improvement. But it is not visible on the outside.
Being the open source pioneer that Ultimaker is, how has the role of the open source community changed since the company first started?
Heiden: In reality, the contribution to hardware is virtually gone. The reality is it’s too difficult now. The same goes for firmware. But on the Cura side, it’s still very strong. And people contribute, think, help, and slowly, we will see more contributions in the field of materials. I’m pretty sure about that. But at this point, I feel that you must be a very good engineer and very well aligned with the whole team of builders of a machine to really contribute something to hardware.
With an increasing focus on the professional market, do you ever see Ultimaker expanding beyond desktop FDM 3D printing?
Heiden: FDM is what we understand and what we’re best at. That means that what we now see is customers asking for standardization. What they’re looking for is that not just support in the early development but also with producing functional prototypes. That’s something we’re certainly aiming for. The other thing we aim for, once you are able to deal with functional prototyping, is that you’re able to handle spare part production in a distributor fashion, where you simply make it wherever it is needed.
If we’re able, within say five years, to deliver those parts in the product life cycle and, on the other hand, deal reliably with this material variety, I’d say we did an awfully good job.
As someone who has sort of been in the scene since the early days, how have you seen it evolve for better and for worse? How do you think the 3D printing industry has changed?
Wijnia: I have seen the hype as actually being true. And I think it was my biggest insight with all phases of the hype going down, then picking back up. And we are now really on the way up. In the last seven years, it’s like we grew the company. When I first started, I had plenty of time to fiddle around and play around. Now, I have three kids. I don’t have 15 minutes per week for myself. So, I’ve realized that the whole promise of making everything at home is not true.
And it will not be true until 3D printing will be good enough to actually produce products instead of parts. And the whole industry is not there yet. So, I’ve been driving up and down to the office and wondering why the printer at home is not running. And that was just because the printer was the problem, but also making designs for a part that I needed in the house was a problem too.
And I see with the Volkswagen business case, the price point of the materials, price point of the machine and the speed in which a part is printed right now, it brings added value. But a business case does not exist, if the price of the machine is 10 times as high like the industry levels are there with a price point of materials 5 times as high. Then, the business case is not there anymore. But having that business case out there, it actually works. And that is going to be the fly wheel for making it more professional. We can’t walk this path without a business case. That’s what I also learned. So, I’m very glad this actually is happening, it’s flying off, it’s taking off.
I really think that there is a lot of added value in 3D printing. But we also have to do a lot of further research and development in all of these technologies to make that real.
Website: LINK
Schreibe einen Kommentar
Du musst angemeldet sein, um einen Kommentar abzugeben.